HMD Kontro is delighted to be sponsoring our team member Neil Jessop again this year in the Modified Ford Series. Motor racing is an expensive sport and Neil says the financial support he gets from the company is a huge help. The series is growing every year and the provisional calendar, consisting of nine races has already been published with the first race at Silverstone scheduled for 20 March. The racing is starting much earlier than last year, so it must be a good sign that we are moving on from Covid.
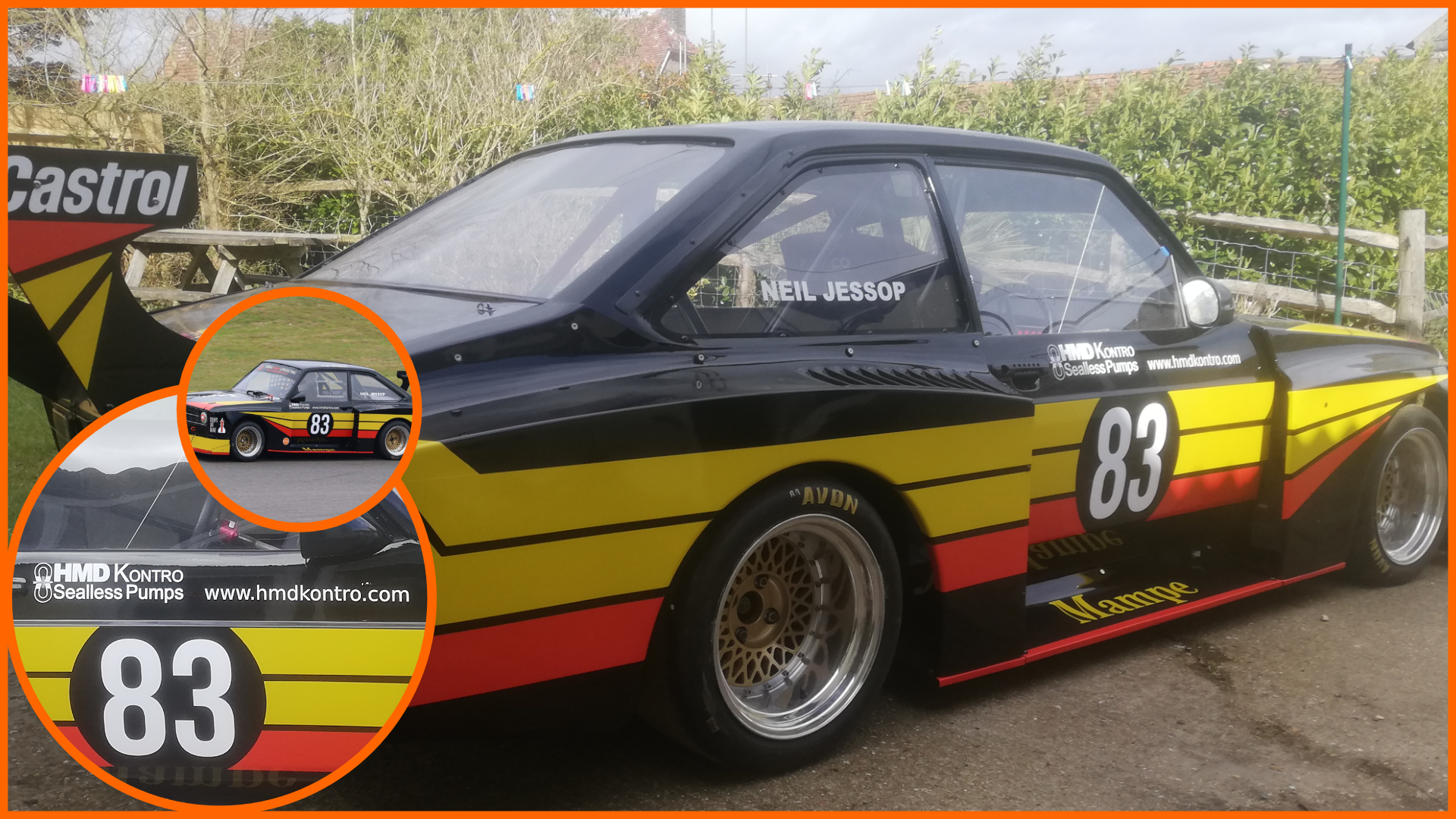
Changing the suspension geometry for faster lap times
During the racing season Neil admits that there are always mechanical issues with the car, some more major than others, with some jobs being able to be put off until winter. These include issues that are either not that critical or an improvement is required that will be a big job and cannot be fitted in between meetings. This means Neil has been working through the small jobs over the winter period. He has also had his hands full changing the suspension geometry of his Ford Escort, to quite a large degree, involving new suspension components and altering the car itself to make it all fit. This is aimed at giving the car more grip on the track for even faster lap times.
Brands Hatch, Silverstone, Donington and Snetterton
Neil is hopeful he will be racing at the first meeting although he is currently on the reserve list for the event at Silverstone, as the grid is oversubscribed. His plans include racing at six of the meetings, namely:
- Silverstone – 20 March
- Brands Hatch – 9-10 April
- Donington – 28 May
- Snetterton – 23-24 July
- Brands Hatch – Ford Power Live – 18 Sept
- Brands Hatch – Formula Ford Festival – 22-23 October
This means he will only be missing out on Knockhill, Cadwell Park and Oulton Park, which are the races that are furthest away from Neil’s base in East Sussex.
Staying fit and eating healthily are all part of the job
Neil puts a lot of effort into staying in shape, as he believes this gives him an advantage over his fellow competitors. That hundredth of a second can make the difference between winning and losing! He also believes if you get tired during a race, you can lose concentration and make mistakes. The secret to staying fit is actually enjoying it and Neil has been participating in CrossFit for many years. This is a combination of strength and conditioning which involves Olympic weightlifting, powerlifting, gymnastics, running, rowing and more. CrossFit advocates sound nutrition and Neil incorporates a good diet into his healthy lifestyle.
The mechanics of the Ford Escort
Although Neil’s Ford Escort is a classic, everything on it is built to modern specifications. The engine is a modern all aluminium 2 litre machine that you would typically find in a new Ford Focus or Mondeo. However, it has been rebuilt to include lots of racing parts to produce around 280bhp. The car has a 5 speed racing gearbox with the shock absorbers having been custom built by an American company.
Wheels and tyres designed for speeds of 140mph
The wheels are custom alloys specially designed for the car. Tyres are Avon racing slicks, which take up a big part of the budget, but are worth the expense as they make a massive difference to the performance of the car. They are the only bit touching the track so all the other modifications would be wasted if inferior tyres were used and with speeds reaching up to 140mph, depending on the circuit, good tyres are a must. The tyres actually cost £360 each and last for about three to four meetings depending on the circuit surface with some race tracks being more abrasive than others. Another salient factor on wear and tear is the weather with hot conditions causing tyres to lose their edge more quickly.
Before and after a race
The pre race procedure usually involves travelling the day before the race and staying in a hotel close to the circuit. As you might expect, a lot of Neil’s friends are keen on racing so he has help when going to an event. However, even when things go well at the race, there is still a lot to do including some fine-tuning before the next race, but hopefully no major mechanical work.
HMD Kontro wishes Neil every success in the Modified Ford Series
We would like to wish Neil every success this year and we look forward to hearing all his racing news. We aim to keep you informed throughout the season and of course if you are near to any of the circuits, we hope you might go along to support Neil racing his shiny black 1978 Ford Escort Mark 2 classic car. It really stands out with its new livery including red and yellow stripes and white HMD Kontro branding.