Process Industry Informer is a leading magazine for managers and process engineers working in the chemical, food and beverage, pharmaceuticals and utilities industries. They run an active podcast channel. In a recent episode David Clark, our Senior Engineering Manager, discusses the evolution of magnetic drive sealless pumps, from their introduction by HMD Kontro over seventy years ago to the very latest developments and materials that are driving the industry forward.
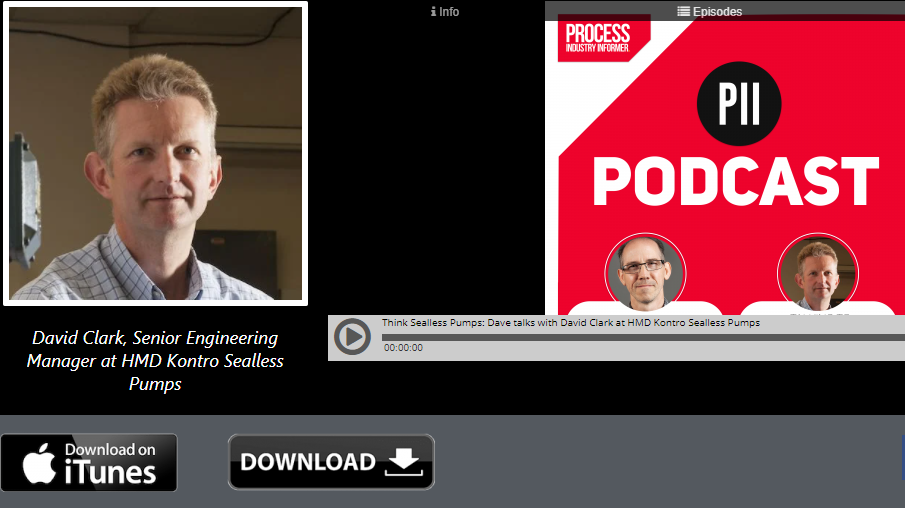
He reports how a step-change in design, driven by technology advances and innovative materials has seen the emergence of a new level of agility and flexibility while future-proofing products against ever-more stringent regulations.
The topics included in the podcast
- Industry compliance – meeting ASME/ISO/API standards
- Innovations including new bearing technology and use of composites
- CSA/CSI launch – a complete redesign to meet current and future needs
- The necessity to get products to the market more quickly
- Future requirements for sealless magnetic drive pumps
- Greener production – energy efficient savings of 15-20%
HMD Kontro has always been at the forefront of innovation, which is aimed at delivering what the industry needs. These include:
- New bearing technology and use of composites: The last ten years has seen the advent of new materials including composites to increase the efficiency and reduce the heat being put into pumps to increase their overall robustness.
- Silicon carbide and ceramic matrix composites: Silicon carbide has been used for over twenty years. However, over the last five years, there has been a move to use ceramic matrix composites as an alternative. This further improves the robustness of the pump.
- PEEK composite materials: HMD Kontro produced the ZeroLoss containment shell made from PEEK composite materials almost ten years ago. This provides a more efficient and robust alternative to traditional metallic containment shells.
The CSA/CSI Launch – A complete redesign to meet current and future needs
The catalyst for change and the development of the new range was aftermarket feedback and user comments combined with many years of experience. This led to the complete redesign of an existing product to meet current and future industry needs, involving going back to the drawing board as just a product ‘refresh’ was not going to go far enough.
A complete rethink was needed, resulting in the incorporation of the best of existing pump knowledge combined with new materials, technologies and insights. The result is a range of highly flexible pumps, which are totally configurable with the end user receiving delivery of pumps quickly, often within days.
The pumps can be brought to the market faster thanks to a modular design and configured kits of parts, allowing maximum flexibility in specification and interchangeability to minimise stockholding and to deliver shorter lead times.
Greener production
At the same time, new approaches and materials have been harnessed to improve energy efficiency by 15-20% combined with the peace of mind from total containment, as well as assisting in predicating performance issues.
How does the future look for sealless magnetic drive pumps?
There is more and more acceptance of the magnetic drive sealless pump and the future will see a demand for larger pumps with parts such as internal bearings needing to be bigger and this will demand investigation of further alternative bearing materials. Containment shell technology is seeing more acceptance, including ZeroLoss and non-metallic shells. It is expected that HMD Kontro will continue to innovate and move the industry forwards.
To listen to the podcast, please visit: https://www.processindustryinformer.com/thinking-sealless-pumps